Amidst the worldwide transition towards climate-conscious initiatives, electric vehicle developments have emerged as a key strategy to reduce carbon emissions. The momentum of this movement is exemplified in numbers: electric car sales crossed the ten million threshold in 2022, marking a 55% surge compared to the previous year.
While EVs open a pathway to decarbonize the mobility and transportation sectors, they are reliant on batteries to power their operations, and these inevitably possess a finite lifespan. As EV adoption continues its upward trajectory, a question lingers: what happens to these batteries when they reach the end of their useful life?
Several types of batteries can be used to power EVs, but LFP batteries are an option increasingly utilized by major EV players like Tesla and BYD. Their rise in popularity spans from their lower toxicity levels and affordability as compared to traditional lead-acid batteries.
However, LFP batteries are composed of the same critical minerals, such as lithium and graphite, which are also used in the production of laptops and mobile devices. Battery manufacturers, therefore, face challenges in meeting the increasing demand for batteries.
One possible solution to solve this issue is the recycling of LFP batteries. Current methods of LFP battery recycling involve the use of hydrometallurgy and pyrometallurgy techniques, which are not always environmentally friendly. These two methods involve chemical solutions and heat respectively to purify and extract metals like lithium.
In contrast, NEU Battery Materials has developed an extraction method that adopts a technique called electrometallurgy, entailing the use of an electrochemical separation process to extract battery-grade lithium, a valuable resource that can be reintegrated into the production of new batteries.
According to Bryan Oh, CEO of NEU Battery Materials, this method places a stronger emphasis on sustainability due to its ability to operate under standard atmospheric pressure and room temperature conditions. The utilization of a proprietary solution capable of self-rejuvenation after material extraction also reduces wastage, further amplifying this commitment.
The origin of this technology traces back to research on redox technology that was initially conducted at the National University of Singapore. Insights from the research were subsequently adapted to develop NEU Battery Materials’ proprietary solution that can effectively separate lithium from other battery components.
When black mass—the byproduct after an LFP battery is crushed and dismantled—is placed in a reactor with NEU Battery Materials’ solution, electricity aids the occurrence of electrochemical separation, facilitating the movement of lithium ions across the membrane. This generates two outputs: lithium and hydrogen.
The lithium is extracted and sold to battery manufacturers, enabling reuse for various lithium-based battery types.
NEU Battery Materials operates on two business models. Its clients can either license its technology and integrate the recycling technology into their own facilities, or purchase lithium recycled by NEU Battery Materials within its own facility.
Furthermore, the company has designed its solution to be modular and scalable, accommodating the anticipated surge in EV battery influx.
A greener recycling method
The primary benefit of NEU Battery Materials’ separation technique resides in its low energy consumption. By minimizing the use of acids and heat in the separation process, its approach curbs the generation of pollutants and cuts costs.
While the company’s current focus is to upscale its process, Oh envisions integrating renewable energy sources to power its recycling process to further maximize its net environmental benefits.
From a broader perspective, Oh also shared that, while extending the usage lifespan of electronics is a viable way to improve sustainability, there is ultimately a limit to battery lifespans.
“These bulky EV batteries present a significant challenge as they frequently end up in landfills if not handled properly. Our task is to extract the valuable materials from these batteries and reintroduce them into the supply chain. This practice embodies the essence of circular economics: redirecting materials that would otherwise contribute to landfill waste,” Oh said.
Furthermore, battery manufacturing processes may produce a percentage of batteries that do not meet quality standards, and these present an immediate opportunity to reclaim and recycle their raw materials.
Navigating its challenges
The journey is not without its challenges. As NEU Battery Materials endeavors to scale up its processes, transitioning from a laboratory-scale operation to a full-scale recycling plant appears inevitable.
“We’re tasked with harmonizing our innovative approach with the practical demands of large-scale operations, which requires a deep understanding of various engineering and operational intricacies. Our team’s collective expertise lies in crafting this transition, ensuring that the cutting-edge technology we’ve developed in the lab translates seamlessly into a robust recycling plant,” Oh said.
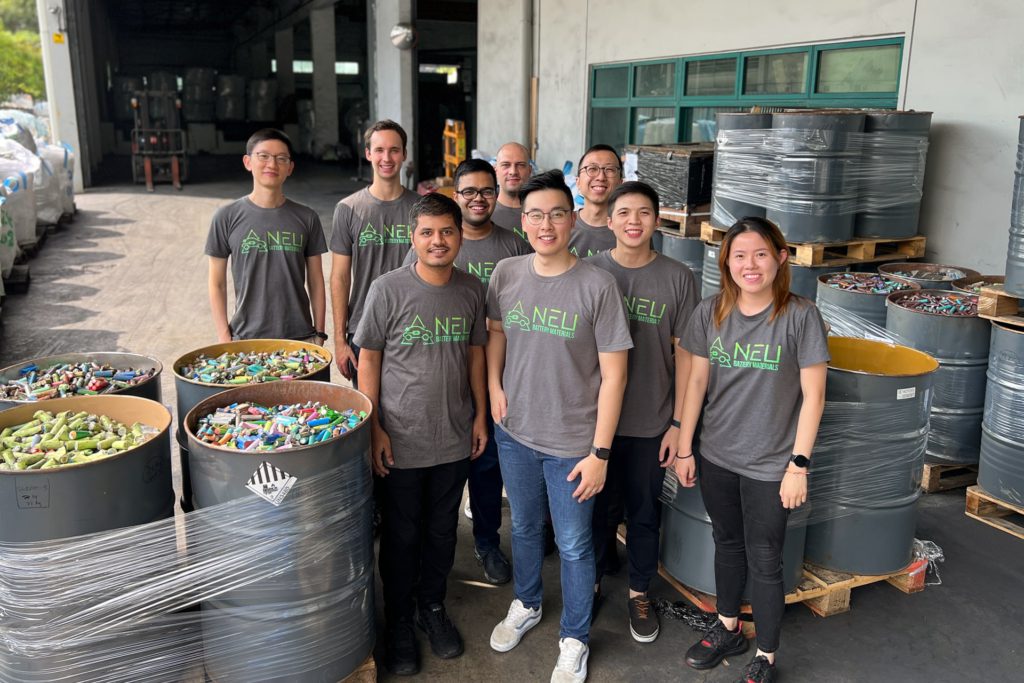
Future outlook
Looking ahead, NEU Battery Materials has been securing collaborations and support from various organizations. It recently established a facility within the battery crushing premises of Secure Waste Management, a company specializing in the recovery, recycling and repurposing of electronic waste.
While continuing to broaden its reach globally through ongoing discussions and collaborations with key industry players in Europe, the company also remains committed to improving its operational efficiency in Singapore. Its current objective is to automate its process line, which will be a pivotal step towards streamlining its recycling efforts.
In addition, NEU Battery Materials is gearing up for the Lee Kuan Yew Global Business Plan Competition (LKYGBPC), scheduled to take place from September 11 to 15, 2023.
“We’re keenly aware that within this competitive landscape, there’s a diverse array of key players, including startups and established corporate partners. For us, this event serves as an ideal platform to not only present our company and our groundbreaking technology but also to engage with a wide spectrum of individuals and organizations,” Oh said.